BUSINESS
French student backlash scuppers ‘Big Brother’ connected bed plans
A French firm has been forced to abandon a pilot project to test connected beds - which transmit real-time information on what’s going on in the sack - after the students they were to be tried out on complained of Big Brother tactics.
Published: 8 September 2017 13:56 CEST
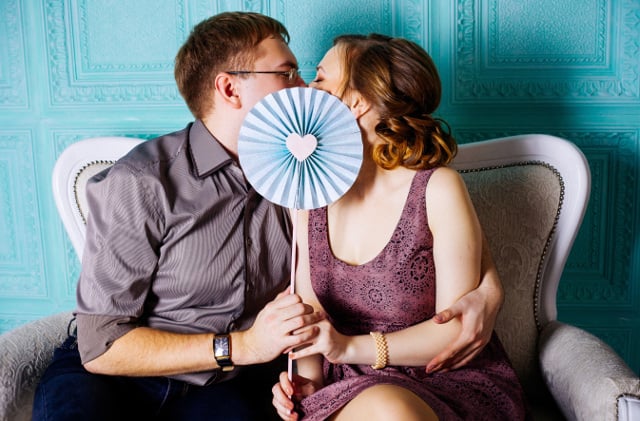
Pexels
Espace Loggia, a designer of space-saving furniture, had put sensors in ten of the 150 foldaway beds installed in the nine square-metre rooms of a newly renovated student residence in Rennes, the capital of the Brittany region.
The connected beds when not in use could be hoisted up to the ceiling, leaving the student space to work at his or her desk. Sensors were placed in the beds that transmit data that enables the company to know if there is a technical problem.
“If a student uses the bed to do pull-ups on, or if the mattress is used as a sofa for ten people, then we know about it,” Paul Malignac, the boss of Espace Loggia, told Ouest France.
He did not specifically mention that the sensors would likely also be able to detect sexual activity, but that may well have been foremost in the minds of the students who expressed their deep concern to the daily regional paper.
“It’s like being spied on,” said one, while others complained that they had not been informed of the project.
The scheme quickly sparked a minor media outcry, and Malignac on Friday told Ouest France that “we don’t want to police students in their bedrooms” and that the sensors were merely to make sure the beds were kept in good shape.
Artisans IoT, the company that made the connected beds for Espace Loggia, said they had not been put into service and would only have been tested on students who gave their consent.
But CROUS, the authority in charge of the student residence, said that it was nevertheless ditching the project.
“We are just as scandalised as them (the students)” about the possible misuse of the technology, it said in a statement.
Url copied to clipboard!